
【Domestic Papers】Influence of temperature on the performance of ε-Ga₂O₃-based surface acoustic wave delay lines
日期:2025-07-10阅读:40
Researchers from the Sun Yat-sen University have published a dissertation titled "Influence of temperature on the performance of ε-Ga2O3-based surface acoustic wave delay lines" in ICAPMS 2025.
Project Support
This work was supported by the National Key Research and Development Program (No. 2023YFF1500700), the Research and Development Plan Project of Guangdong Province (No. 2021B0101300005) and Guangdong Basic and Applied Basic Research Foundation (No. 2022B1515120081).
Background
Nowadays, surface acoustic wave (SAW) devices have been extensively applied in temperature, chemistry, pressure, gas and microfluidics sensors. Traditional passive SAW sensors are based on two-port delay lines or single-port resonators, which are compatible with antennas to form a wireless system. Compared with other types of sensing, wireless SAW technology is an effective solution in some hostile environments, such as underground detection, remote telemetry and aerospace platforms. Today, SAW devices have been increasing adopted in various systems thanks to their miniaturized size, excellent sensitivity and stability.
In this work, the propagation loss of ε-Ga2O3 is extracted from the scattering parameters of SAW delay lines. The temperature dependence of center frequencies, coupling coefficient (K2) and insertion loss are also studied. The experimental results demonstrate ε-Ga2O3 to be a promising contender for temperature sensing application.
Abstract
With the mature advancement of wireless sensing, the requirements for highperformance surface acoustic wave (SAW) devices keeps booming. Epsilon-phase gallium oxide (ε-Ga2O3) has been identified as a promising semiconductor due to its wide bandgap and strong piezoelectricity. In this study, the propagation loss, coupling coefficient (K2 ) and temperature coefficient of frequency (TCF) are extracted from the ε-Ga2O3-based SAW delay lines. The propagation loss of ε-Ga2O3 is extracted to be 0.04596 dB/λ at 1286 MHz for Rayleigh mode and 0.10986 dB/λ at 2083 MHz for firstorder Sezawa mode. The TCF of ε-Ga2O3 for Rayleigh mode and first-order Sezawa mode are determined to be -69.0~-60.0 ppm/℃ and -57.5~-50.1 ppm/℃, respectively. K 2 of ε-Ga2O3 is extracted to be ~1.0%. Both K2 and insertion loss of ε-Ga2O3-based SAW delay lines keep stably varying as the temperature rises to 100℃. The superior K2 performance and good temperature stability indicate ε-Ga2O3 a promising material for application in high-performance temperature sensing systems.
Conclusions
In this work, ε-Ga2O3-based SAW delay lines were fabricated with different free-space gaps. Propagation loss, TCF and coupling coefficient (K2) of the devices are extracted from scattering parameters. The propagation loss of Rayleigh mode is extracted to be 0.04596 dB/λ at 1286 MHz and for first-order Sezawa mode is 0.10986 dB/λ at 2083 MHz. The TCF of ε-Ga2O3 for Rayleigh mode and first-order Sezawa mode are determined to be -69.0~-60.0 ppm/℃ and -57.5~-50.1 ppm/℃. ε-Ga2O3 possesses a higher coupling coefficient K2 (~1.0%) than the traditional AlN/sapphire structure (~0.2%) and exhibits excellent temperature stability. The insertion loss of ε-Ga2O3-based SAW delay lines keeps stably varying as the temperature rises to 100℃. The large enough TCF value, superior K2 performance, and good temperature stability of ε-Ga2O3 make it a promising contender for application in highperformance temperature sensors.
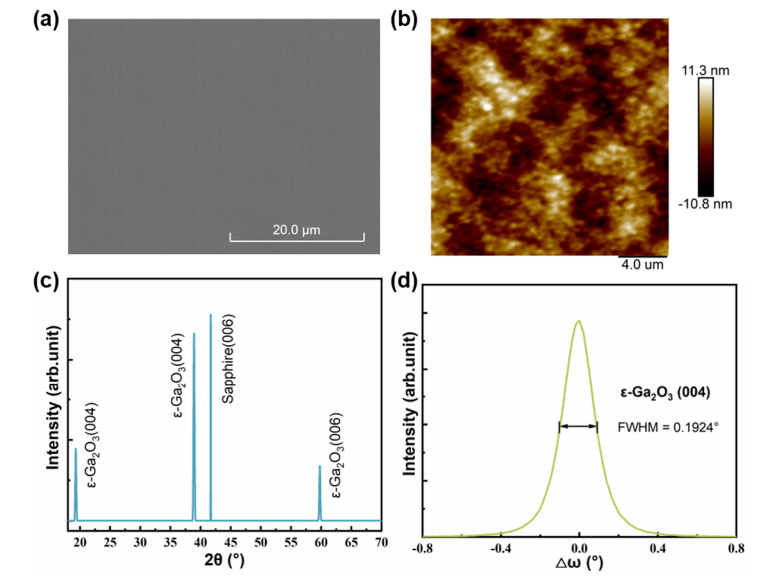
Figure 1. (a) SEM and (b) AFM 2D image of the grown ε-Ga2O3 thin film. Roughness of sample is Rq=3.34 nm. (c) The XRD 2θ-scan and (d) rocking curve of ε-Ga2O3 thin film prepared on c-face sapphire. The full width of half maximum (FWHM) for ε-Ga2O3(004) is 0.1924°.
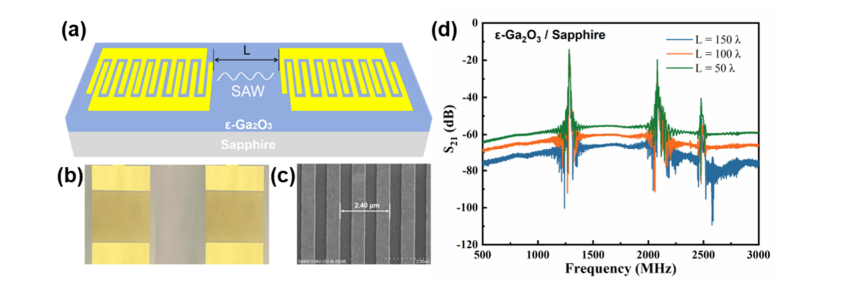
Figure 2. (a) Schematic diagram, (b) optical microscope image, and (c) SEM image of fabricated SAW delay lines based on ε-Ga2O3/sapphire. (d) Scattering parameters of SAW devices with different gaps L.
DOI:
doi.org/10.1088/1742-6596/3030/1/012013